Blogs
Kaizen: The Philosophy of Continuous Improvement for Business Success
The Kaizen philosophy, which means "continuous improvement" in Japanese, is a powerful approach aimed at constantly improving processes, products, and company performance. This method, born in Japan, has been adopted by organizations worldwide to promote efficiency, innovation, and customer satisfaction. This article explores the fundamental principles of Kaizen, its benefits, and how to apply it in your organization to achieve exceptional results.
1. What is Kaizen?
The term "Kaizen" is derived from the Japanese words "Kai" (change) and "Zen" (good). It represents a systematic approach to continuous improvement that involves all members of an organization in the process of perfecting operations. Unlike radical changes, Kaizen focuses on small but consistent improvements, which contribute to significant gains over the long term.
2. Key Principles of Kaizen
Kaizen principles are based on several fundamental concepts:
Continuous Improvement: Kaizen is built on the idea that small improvements, made regularly, can lead to substantial results. It encourages the continuous analysis and optimization of processes.
Employee Engagement: All team members are involved in the improvement process, fostering a culture of collaboration and responsibility.
Process Focus: Instead of focusing solely on results, Kaizen emphasizes improving processes to optimize performance and quality.
Standardization: Once an improvement is implemented, it is standardized and integrated into routine practices to ensure the sustainability of gains.
3. Benefits of Kaizen
Implementing Kaizen offers numerous advantages to businesses:
Increased Efficiency: Continuous improvements help optimize processes and reduce waste, thereby increasing overall efficiency.
Improved Quality: By focusing on process improvements, Kaizen helps reduce errors and improve the quality of products and services.
Employee Engagement: Active employee participation in the improvement process enhances their engagement and job satisfaction.
Flexibility and Innovation: Continuous improvement encourages innovation and allows businesses to quickly adapt to market changes and customer needs.
4. How to Implement Kaizen in Your Organization
To effectively integrate Kaizen into your business, follow these steps:
Evaluate Current Processes: Analyze existing processes to identify areas needing improvement. Use tools like process maps and flowcharts to visualize operations.
Encourage Participation: Engage all team members in the improvement process by soliciting their ideas and suggestions. Create an environment where everyone feels valued and encouraged to contribute.
Implement Improvements: Apply proposed improvements and test them on a small scale before generalizing. Ensure changes are documented and standardized.
Measure Results: Assess the impacts of implemented improvements using key performance indicators. Adjust processes based on results and employee feedback.
Promote a Kaizen Culture: Make Kaizen an integral part of organizational culture by highlighting successes and encouraging continuous improvement at all levels.
5. Success Stories with Kaizen
Many companies have leveraged the Kaizen philosophy to enhance their performance:
Toyota: Toyota is often cited as a prime example of Kaizen with its lean production system. The company uses Kaizen to optimize manufacturing processes, reduce waste, and improve quality.
Sony: Sony adopted Kaizen to improve production processes and develop innovative products. The continuous improvement approach has contributed to its success in the electronics industry.
Honda: Honda uses Kaizen to enhance its manufacturing processes and products. The involvement of all employees in the improvement process has played a crucial role in its global success.
6. Kaizen and the Toyota Production System
The Toyota Production System (TPS) is renowned for its efficiency, thanks to Kaizen principles, which mean "continuous improvement." Kaizen involves all employees, from executives to workers, in regularly proposing and implementing small incremental changes. This approach aims to improve processes to reduce waste, enhance quality, and increase productivity. By continuously refining its operations, Toyota has maintained its leadership in the automotive industry through constant minor improvements that collectively lead to significant gains.
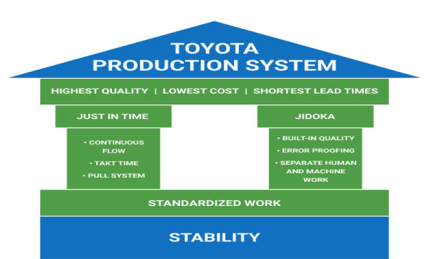
7. Best Practices for Adopting Kaizen
To successfully adopt Kaizen, consider these best practices:
Strong Leadership: Ensure leaders support and promote the Kaizen approach. Their commitment is crucial to inspire and motivate teams.
Continuous Training: Provide ongoing training on Kaizen principles and associated tools to ensure employees have the skills needed to participate actively.
Recognition of Contributions: Value employees' ideas and contributions by acknowledging their efforts and highlighting successes.
Regular Evaluation: Regularly assess processes and results to maintain momentum and ensure improvements are sustainable.
Conclusion
Kaizen is more than just a methodology; it is a philosophy that encourages companies to embrace a culture of continuous improvement. By integrating Kaizen into your operations, you can optimize processes, enhance quality, and strengthen employee engagement. Commitment to continuous improvement can transform your organization into a model of success and efficiency.Sources
Kaizen Institute
What is Kaizen ?